メッキ加工をオリジナルマフラーとシーシーバーに展示品
2019年08月07日
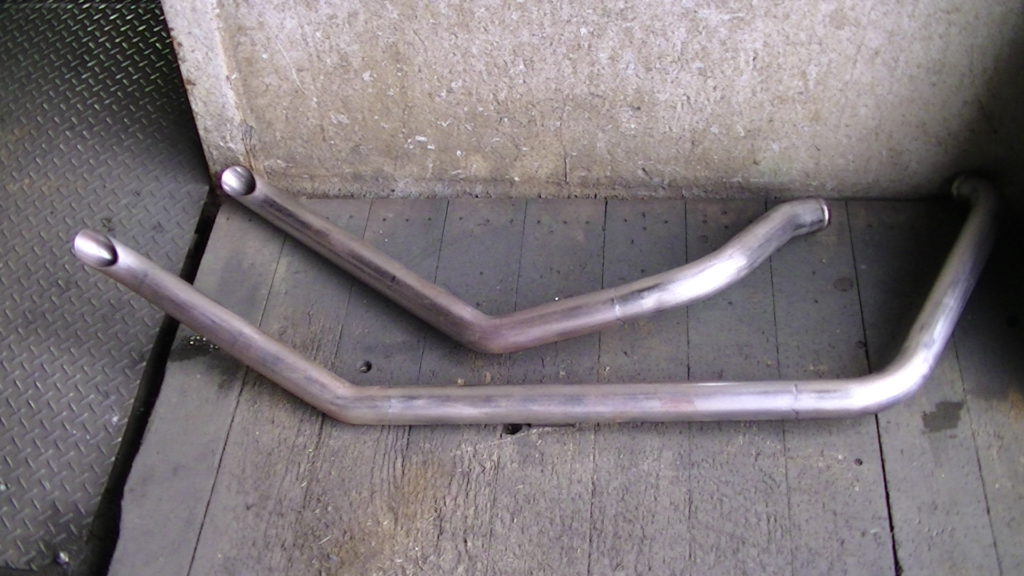
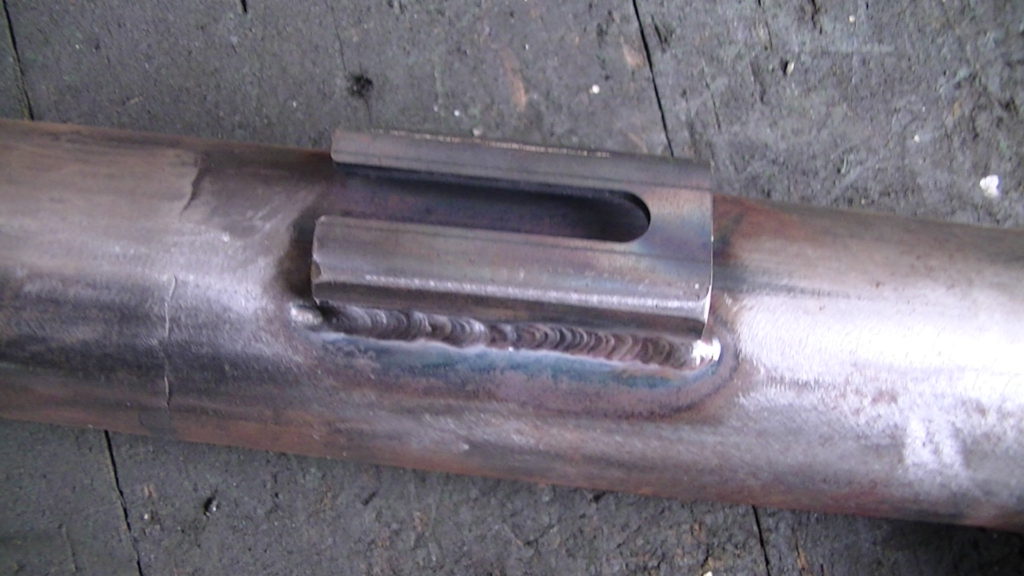
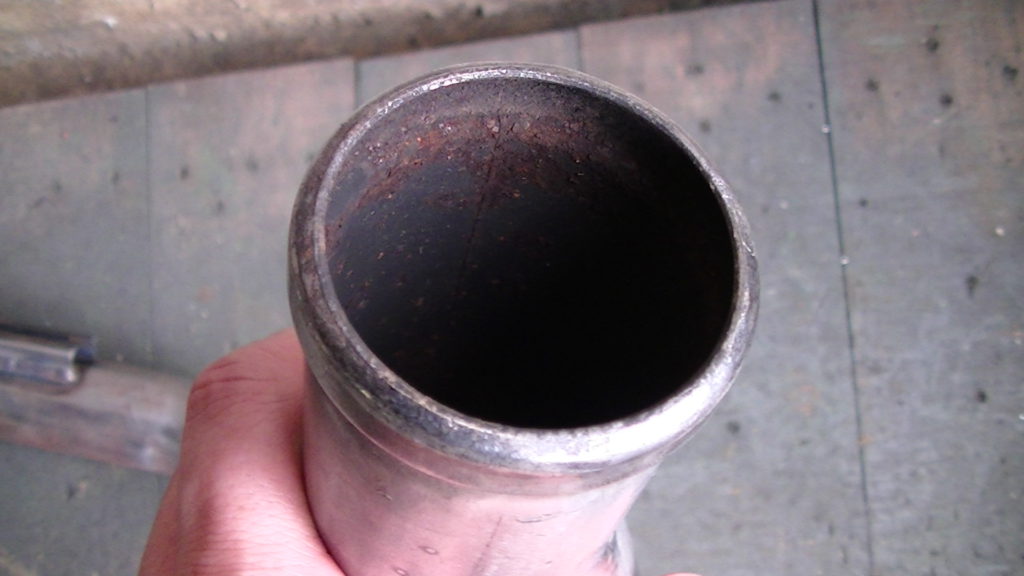
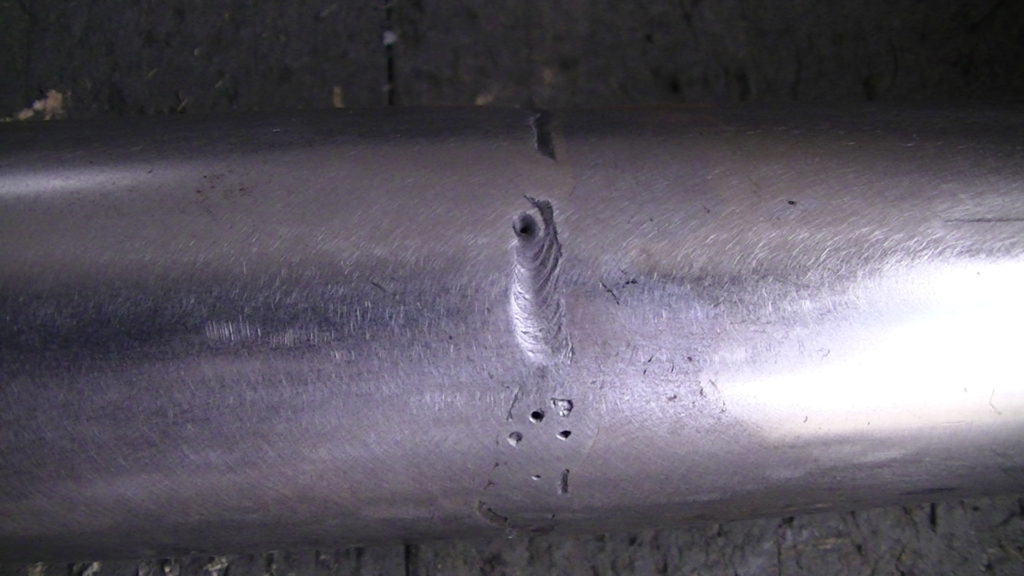
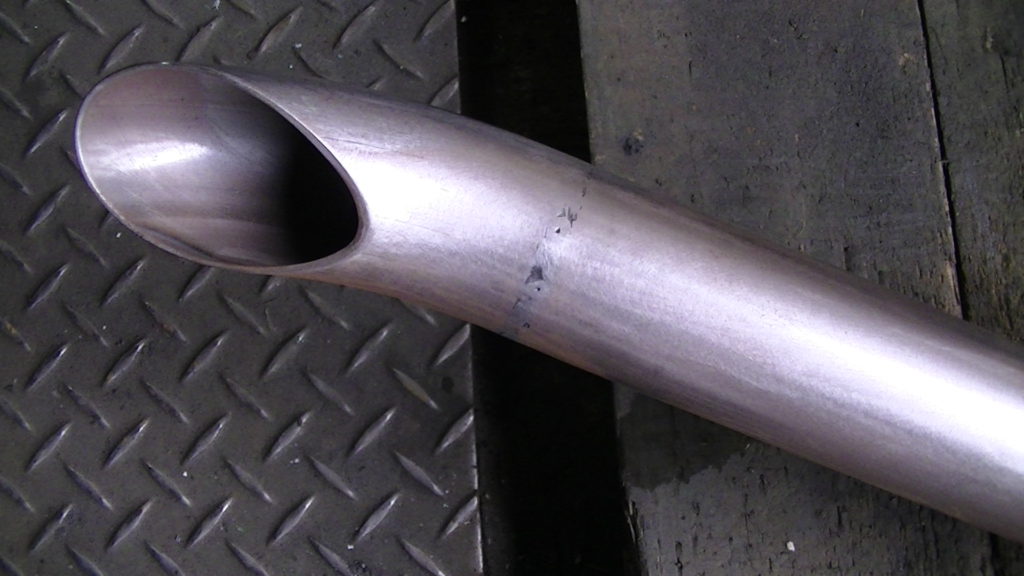
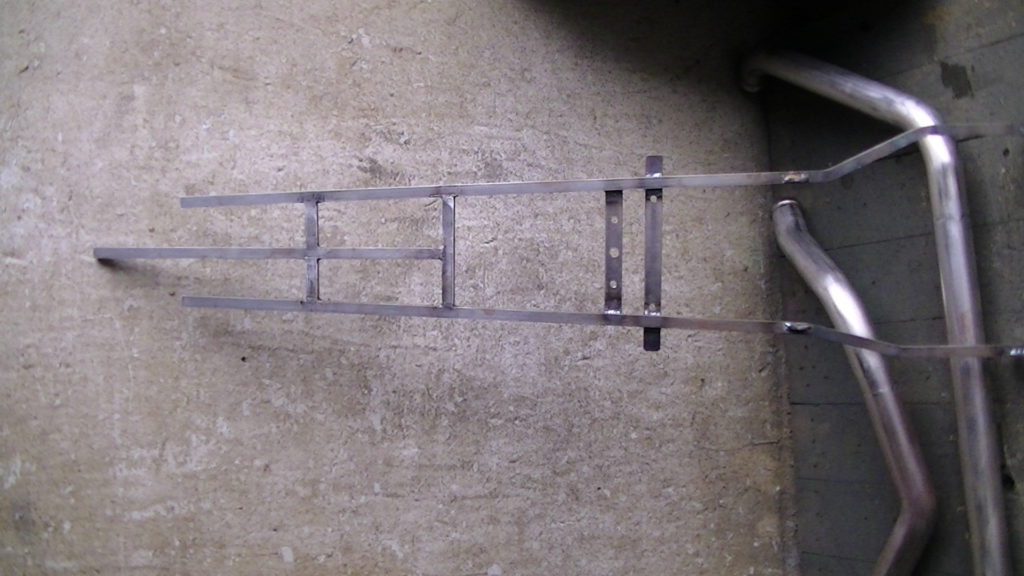
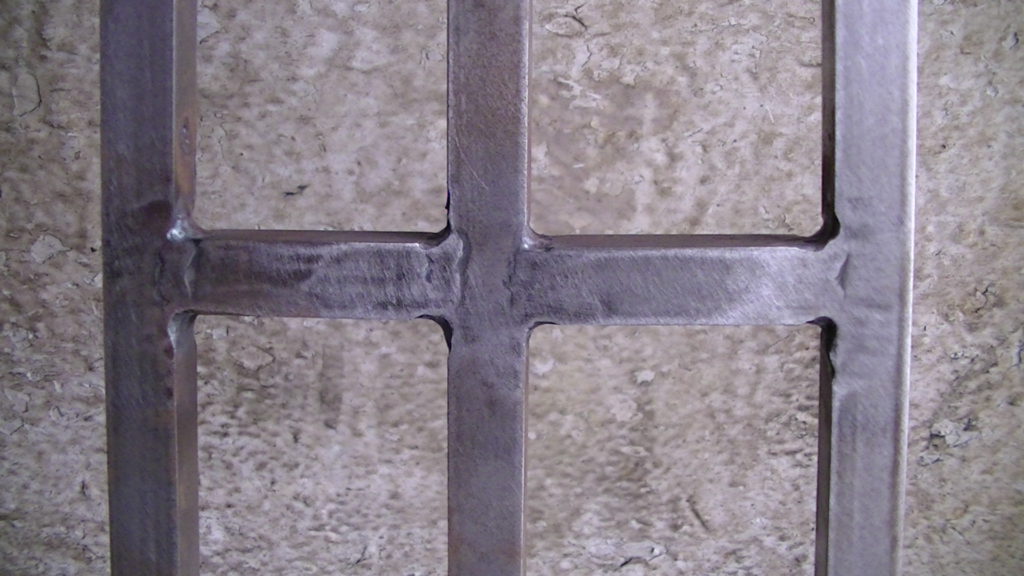
上の写真はバイクカスタム店様からのご依頼でショーに展示する為にオリジナルマフラーとシーシーバーを製作されて弊社にご発送して頂きました。このパーツ全てお客様製作ですのでご覧の様なビフォーになっております。溶接部分が私たちモーター関連のメッキ業者としまして気になる部分です。例えば、この様な溶接部分の穴を埋めるとなると板金加工が必要となります。その板金加工とは真鍮を溶かして埋める方法である、ろう付けになる訳ですがこの様にバイクのマフラーは耐熱温度が非常に高いパーツとなりますので、弊社で行う上メッキ加工は不可になります。耐熱温度が高いメッキパーツの完成を目指すものは弊社の中メッキ加工(分厚いメッキ)か下メッキ加工になります。当然、板金加工はろう付けのみです。注意しなければいけない物として極小の穴にはろう付け板金加工は出来ません。その場合、バフ研磨作業で極小の穴とその横を平らにさせてメッキで分厚くして埋める様にするか、この様な方法で作業を行います。皆様もご承知の通り大量生産型の自動溶接機であるならば綺麗な溶接個所になりますが、オリジナル製品で個人仕上げとなると大変難しくなります。今回のお客様は展示に間に合わせる事を第一条件にされて弊社のメッキランク下メッキ加工を選択されました。弊社の下メッキ加工と言いましても仕上がりは大変に綺麗に仕上がります。しかしながら中メッキ(分厚いメッキ)までの見栄えのクオリティと錆びにくさのクオリティまでは届きません。なぜかと言いますと、メッキ加工で行う薬品や作業が全く別物だからです。例えば、剥離剤は違うものを使いますし、バフ研磨作業も最終番手が全く違います。メッキ液も違いますし、各メッキに漬ける時間も異なります。この様に全ての作業が異なる訳ですからパーツの仕上がりや腐食の速度が違うのも当然と言えます。それでは、オリジナルマフラーとシーシーバーに下メッキ加工を施す方法をご紹介させて頂きます。まず初めに表面剥離を行う為に強酸に漬け込みます。本来、厚メッキ加工でしたらシアンを使用致します。続いてバフ研磨作業ですが下メッキ加工の最終番手は180番手程度です。厚メッキ加工の最終番手は420番手です。必要で有る場合は更に番手を上げて行きます。続いて銅メッキ加工はマフラーの場合は厚メッキ加工も下メッキ加工も行いません。その理由はマフラーの様な高温にさらされる物は銅メッキの下地が溶けてしまいメッキが浮いてきてしまうからです。この様になっては意味が有りません。続いてニッケルメッキですがこれも一発勝負で決めなければ高温でメッキが剥がれやすくなります。最後にクロムメッキですがこれは厚メッキと下メッキでは槽に漬けこむ時間が異なります。
カテゴリ:ブログ