ホンダスティードの経年劣化バイクボトムケースを再メッキ加工
2019年10月31日
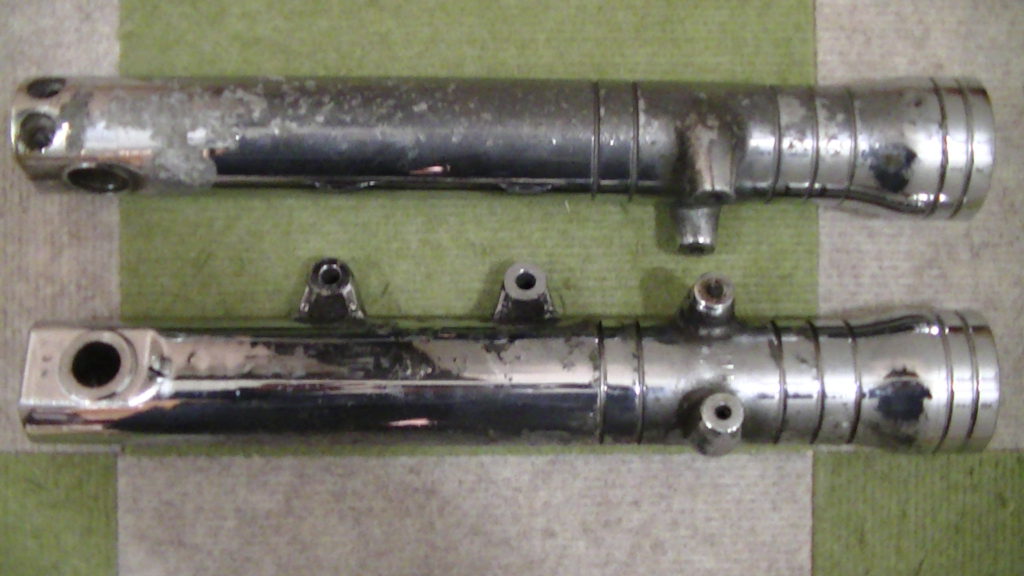
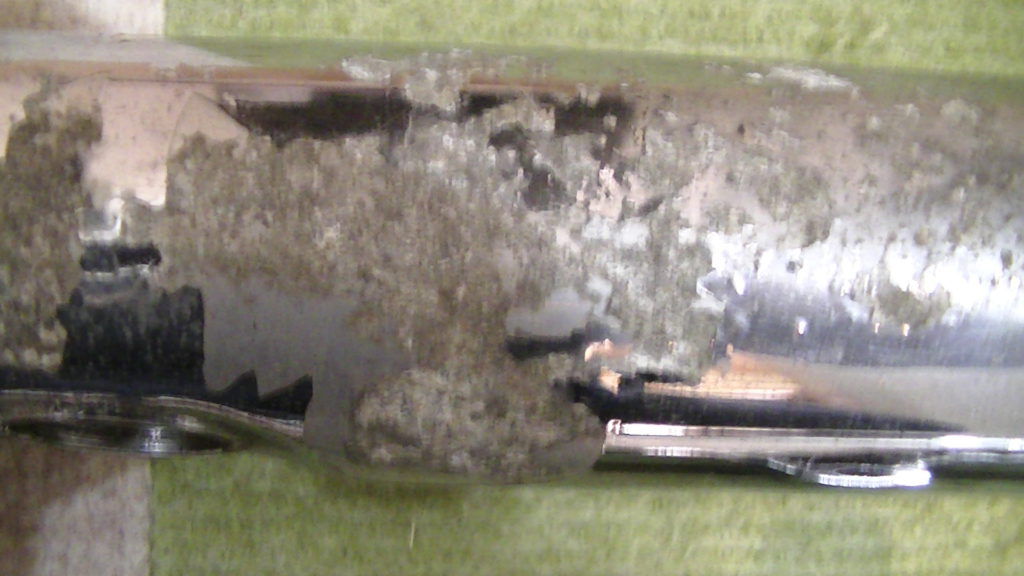
メッキ加工を施す為に、まず確認しなければいけないのが部品の材質です。磁石でくっ付くか?それともくっ付かないのか?ここを確認致しましょう。次に錆びている個所を見て下さい。2枚目の写真の様に見える錆は大抵アルミニウムの材質です。バイクボトムケースの多くはスチールで出来ている事が多いのですが、スチール製部品はこの様な錆では御座いません。黒っぽい誰でも一度は見た事のある錆です。それを思い出してご自分の再メッキ加工したい部品の表面にある錆と比べて見て下さい。自動車の旧車でよく使用されている亜鉛ダイカスト(アンチモニ)の錆はアルミニウムの錆に少し似ていますが、この写真の様にメッキが剥がれてる事はあまり御座いません。錆が盛り上がってボコボコしています。アルミニウム部品が腐食すると錆初めは青っぽい錆が見えたり致します。この様に部品の素材によって腐食した箇所の見栄えが変わって見えます。我々、装飾クロムメッキ加工に携わる者は今までの経験から手に触れて恐らく、この部品はこの素材で出来ていると判断いたします。皆様も、この見方を参考にして頂けたらと思います。それでは今回ご依頼頂いた1990年代のホンダスティードの純正バイクボトムケースの再メッキ加工についてお話しさせて頂きます。先程も言いました様に、この錆から見ても重さを量ってもアルミニウム製のバイクボトムケースと言えます。メッキを剥離して素材表面を観察致します。今までの経験値から上の写真の様な腐食痕はかなり酷い状態になっています。メッキで隠れている個所にもこれと似たような腐食痕があると思います。この場合は出来る限りバフで徹底的に磨き込みを致しますが、新品未使用品程、綺麗に仕上がる事は通常の再メッキ方法では物理的に不可能と言えます。お客様の予算が潤沢にあるのならば、上メッキ加工をお勧め致します。この方法は素材がかなり悪くても表面を補修する事で部品が甦る考え方です。素材の表面を生かしてメッキを施す方法とは全く違う考え方です。このバイクボトムケースのご依頼主様は弊社の中ランクである厚メッキ加工にてリクロームを施して欲しいと言うご希望です。剥離後にバフで磨き込み作業を施して、銅メッキ加工を致します。もう一度、バフ研磨でピンホールを極力埋めて、2回目の銅メッキを分厚めに行います。この時に、ボトムケース表面の腐食痕やピンホールの残りをチェック致しますが、表面がまだ酷い場合は3回目の銅メッキ加工を行う事になります。この作業も厚メッキ加工ならではです。次にニッケル仕上げを行いますがかなり分厚くする必要があります。最後にクロムメッキ加工を施して完成となります。因みに、アルミニウム素材の部品に腐食痕が酷い場合の板金加工は非常に難しく、スチール素材の部品に板金加工する難しさとは次元が違う程です。
カテゴリ:ブログ