メッキ加工部品の状態によって下地修正や板金が必要な状態
2019年10月09日
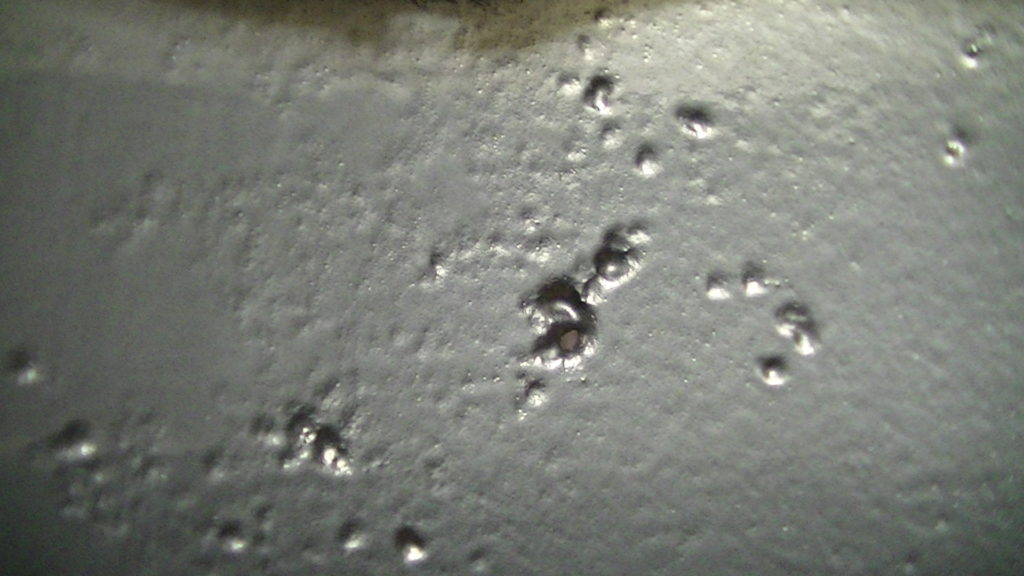
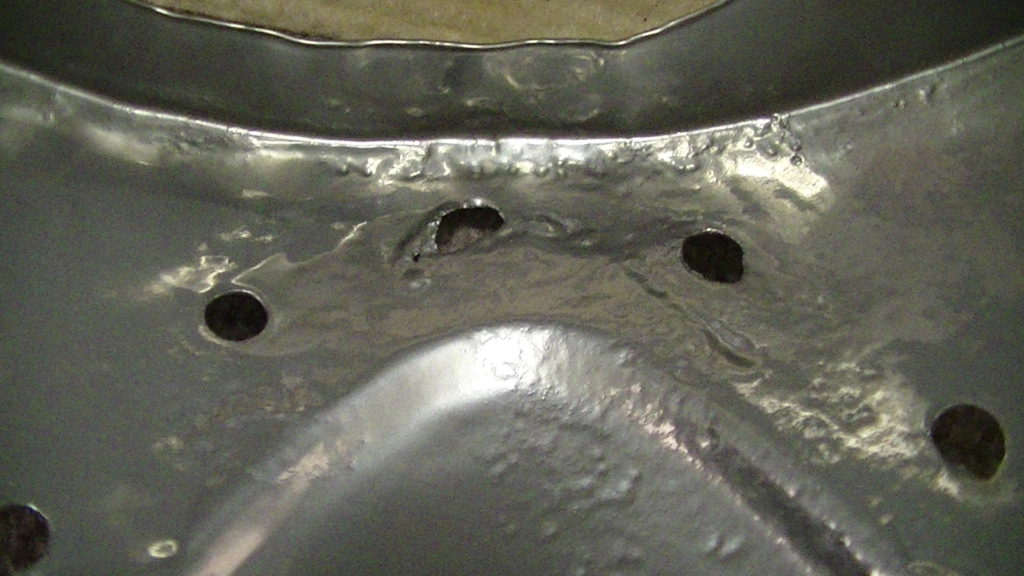
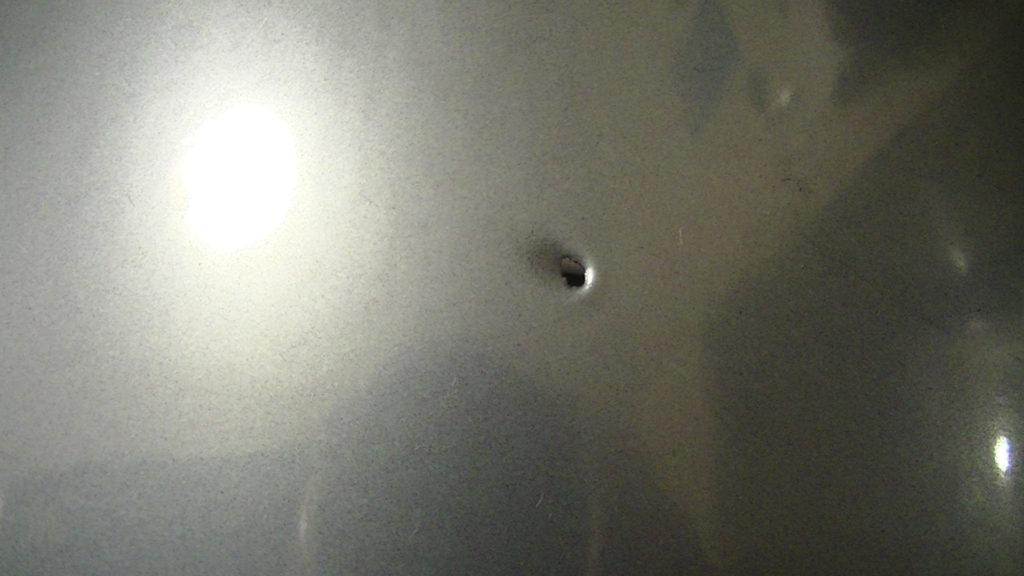
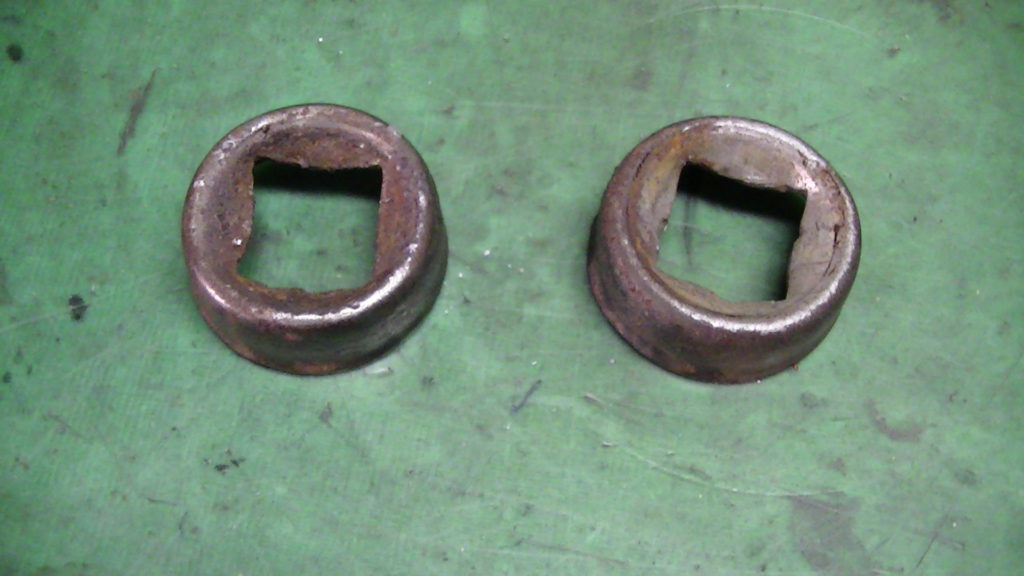
メッキ加工に於いて部品の素材表面を綺麗な状態にしなければ、各メッキ加工で綺麗な完成品が出来ない事は皆様はご承知の事だと思います。今回のお話は、上の写真の様にクロムメッキ加工や他のメッキ加工を施して綺麗な状態で仕上げたいとお考えのお客様がご依頼される前の、部品の状態をご自分で見てこの状態であれば下地修正や板金加工が必要になるのではと分かる様にご説明をさせて頂きたいと思います。そうする事でメッキ加工工賃と別に素材表面を綺麗にする為の下地修正代金や板金加工賃が発生すると言う事が頭の片隅にあると有る程度様々な意味で覚悟する事が出来ます。そして事故などで凹みが生じてしまったバンパーやグリル、様々な部品等には弊社にご発送して頂く前に黒色のマジックなどで円などで囲って頂いたりして印を付けて頂いていますが上の写真の様な経年劣化の腐食痕が気になって特にその部分を綺麗に又は新品の様な仕上がりにしたい場合は凹み部分の印と同様にして頂きますとお客様の見栄えのクオリティがどの程度追求せれているかが分かる為に部品を剥離剤に漬けて素材その物が分かった時に他の腐食痕も綺麗にしなければいけないと職人が分かると言う大きなメリットが御座います。弊社の上メッキ加工をご希望される場合は部品の表面全面を細かな粒子の金属パテで表面補修を施しますのでこの様な印を付けると言う手間は必要御座いませんが厚メッキ加工(中ランクのクロムメッキ加工)を選んで頂いた場合には印を付けるメリットはお客様にとって大きいと思います。上の3枚の写真は60年ほど経った自動車部品です。素材はスチール製でかなりの劣化具合で有る事から塗装を分厚くした上で光沢クリアー塗装でこの様に見栄えを良くした様です。一番上の写真の経年劣化状態は自動車やバイク、トラック等の旧車の保管場所や手入れにもよりますが40年以上時が経っている場合によく見られる事が多いです。この様な経年劣化が多い部品の箇所はバンパーで言いますとコーナーのRがかかっている個所やバンパー上部や下部の雨水が滴る箇所等によく見られる腐食痕です。この様な経年劣化の場合は弊社のろう板金加工を施した上で厚メッキ加工(中ランクのメッキ)を施す事により綺麗な仕上がりになります。続いて2番目の写真は部品が損傷したのか、トンカチか何かで形状を修正されている事が分かります。そしてその周辺は経年劣化によって表面がボコボコした状態になっています。この様な状態でこの部品を新品の様に甦らせる方法は、弊社の上メッキ加工になります。上記で述べさせて頂きました様に細かな粒子のアルミニウム製金属パテで腐食が板金加工でも物理的に綺麗にならない場合部品表面に下地修正を施す事により表面を新たに作り直すと言う加工方法ですので綺麗に仕上がる事になります。3番目の写真は何かに当たって出来てしまった穴です。この場合は一番上の写真の加工方法と同じでろう板金後に厚メッキ加工を施せば新品未使用品の様な綺麗な状態で甦ります。4番目の写真は既にメッキが経年劣化によって無くなっている状態です。部品がこの様な状態になるのは保管状態にもよりますが50年以上時が経っている場合に見られます。この様な場合は新品未使用品の状態をご希望されるのであれば弊社の上メッキ加工を選択して頂ければ新品未使用品の仕上がりになります。上の写真の様に部品の腐食具合によって弊社のメッキランクと板金加工を組み合わせる事でお客様の部品も新品未使用品の様に甦ります。
カテゴリ:ブログ