無電解ニッケルメッキ加工でブロンプトンPステムを綺麗に
2019年08月06日
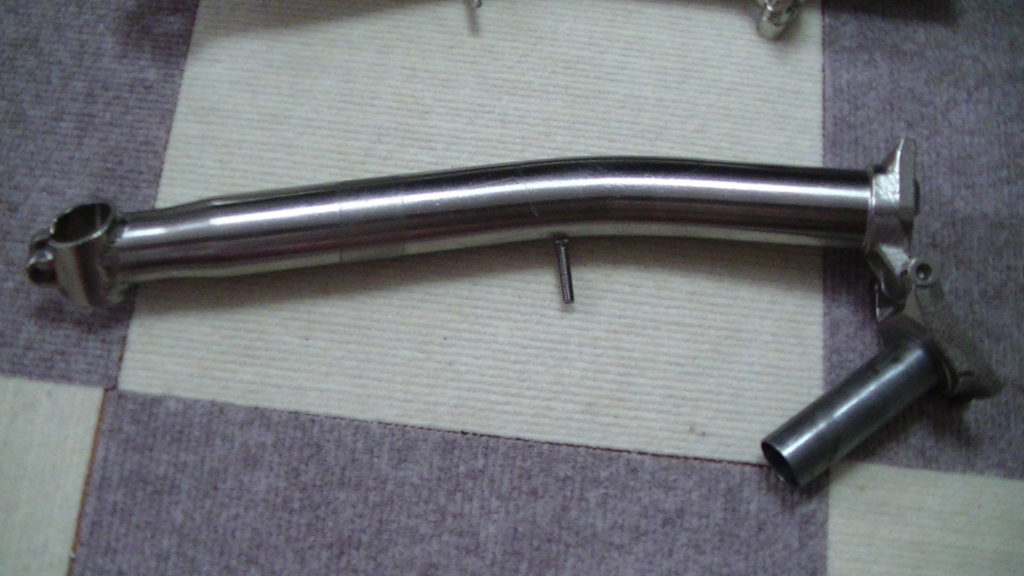
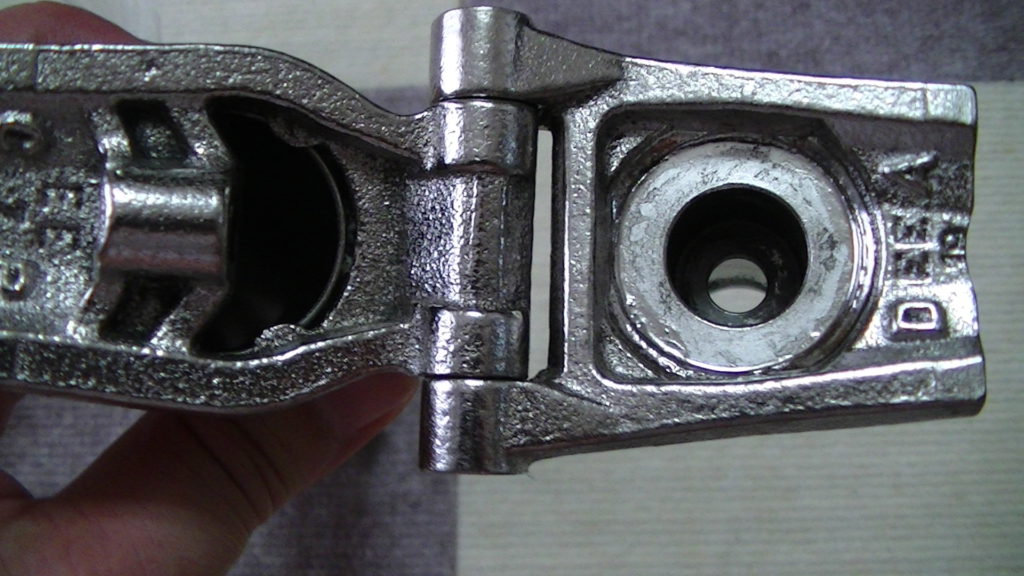

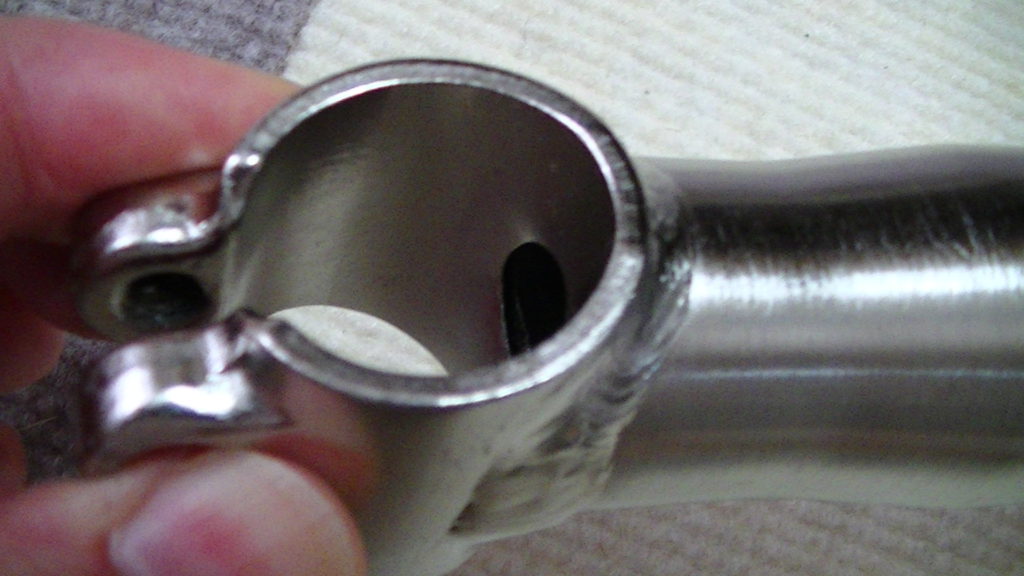
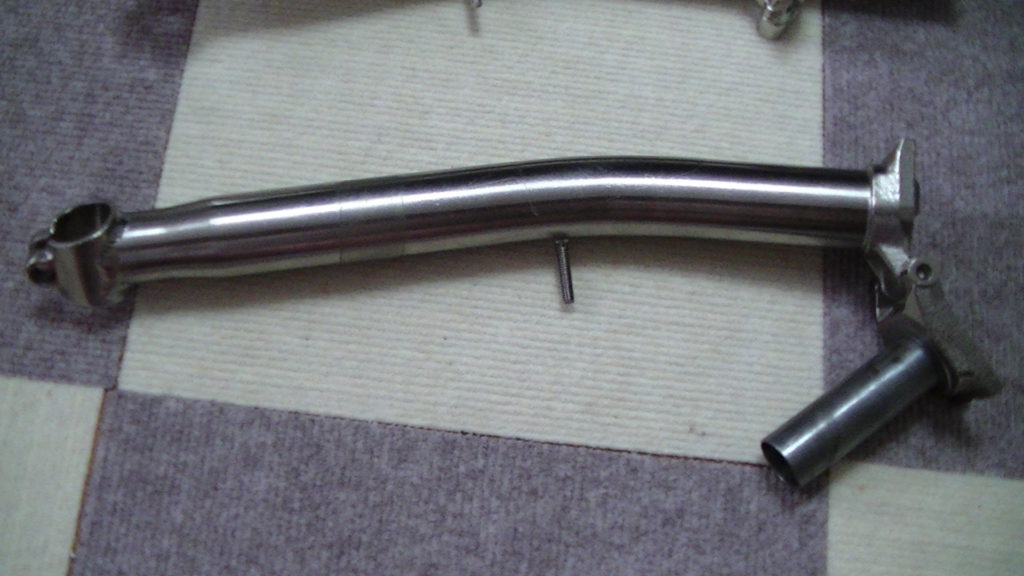
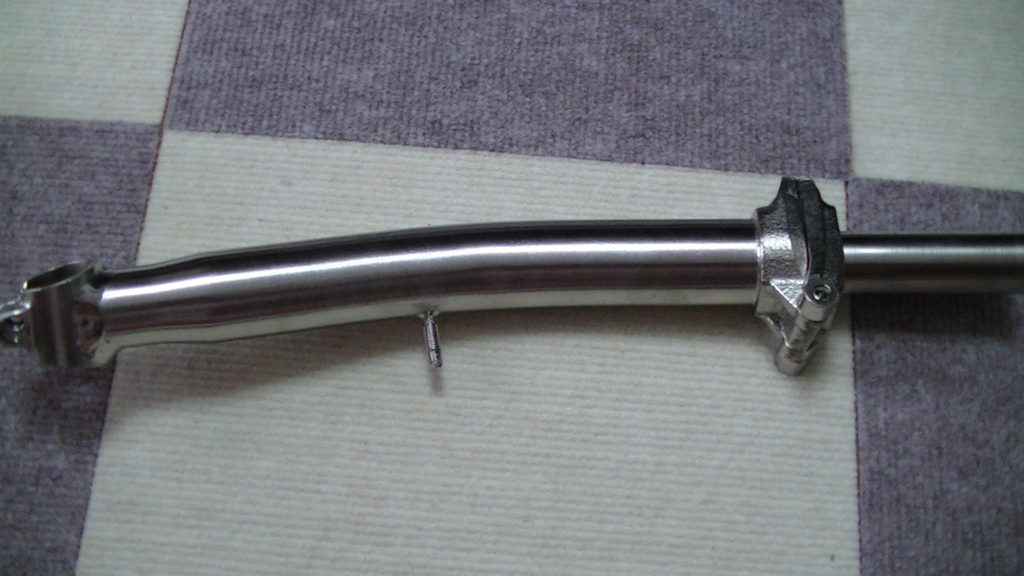
上の写真は無電解ニッケルメッキ加工による再メッキを施した物で下の写真がそれです。品名はイギリスの自転車メーカーでブロンプトン・バイシクル社製のPステムと言う部品です。因みに、このPステムが装着されている自転車は2016年に世界で1500台限定で製作されて、そのうちの150台が日本で販売された希少価値車です。このメーカーは折り畳み自転車の世界的な超有名メーカーです。この会社のポリシーはレーシング的な要素を追求するのでは無くて軽快車や実用的な通勤車に特化した事に徹しています。この自転車の各パーツは上の写真の風合いの無電解ニッケルをコンセプトに用いています。今回、ご依頼頂いたお客様は腐食したPステムパーツを電気ニッケルと勘違いされて知り合いの業者に頼まれたそうです。出来上がりは色の風合いと入り組んでいる個所にニッケルが付いていなかったり、直ぐに錆による変色が出てしまった為に、弊社にご依頼して頂きました。メッキと言いましても数百種類も御座いますので自動車販売店様やバイク販売店様、整備工場の方にはまず分からないと思います。メッキ工場の従業員でも自分の工場で行っているメッキは分かるでしょうが、他社のメッキは分からない様なレベルです。だから普通分かる訳がないと言うのが当たり前です。その為にも弊社の様に自動車やバイク、トラック、自転車等のメッキに特化した業者を選択される事が失敗しない事になります。このPステムを弊社にサンプル品と一緒に送ってきて頂くようにお客様に伝えさせて頂きました。その理由は、元々のメッキがどのメッキなのかを確認したかったからでした。他社で失敗したPステムには剥離して違うメッキが付着しているので元々のPステムのメッキが分からないのではお客様の要望にお答えする事が不可能になる訳です。サンプルを見た時に直ぐにメッキの種類が分かりました。サンプル側のPステムには無電解ニッケルメッキが施されていて、他社で失敗しているPステムには電解ニッケルメッキが施されている。違いは色合いは素人では分かりにくいですが、稼働する部分や入り組んだ部分のメッキの付着具合が全く違う事にきずきました。電解ニッケルは無電解ニッケルと違い錆びる速度が全く違いますしニッケルが入り組んだ箇所に付きやすいのも無電解ニッケルメッキです。だからこの自転車を作っているブロンプトン・バイシクル社は無電解ニッケル仕上げをされたのだと思います。ニッケルはクロムよりも光沢は低いです。その上で部品の入り組んである箇所にニッケルが付着していたら無電解ニッケルメッキ加工でほぼ間違いないと言えます。
カテゴリ:ブログ